Compressed Air Controls
Compressed Air Leaks
Leak Detection
How to Fix Leaks
Maintenance
Compressed air systems account for $1.5 billion per year of U.S. energy costs and .5%
of U.S. emissions. Many industries use compressed air systems as power sources for tools
and equipment for pressurizing, atomizing, agitating, and mixing applications.
Optimization of compressed air systems can provide energy efficiency improvements of 20%
to 50%.
Compressed Air Controls
Compressed air system controls match the compressed air supply with system demand
(although not always in real-time) and are one of the most important determinants of
overall system energy efficiency. Proper control is essential to efficient system
operation and high performance. The objective of any control strategy is also to shut off
unneeded compressors or delay bringing on additional compressors until needed. All units
that are on should be run at full-load, except for one unit for trimming. Compressor
systems are typically comprised of multiple compressors delivering air to a common plant
air header. The combined capacity of these machines is sized, at a minimum, to meet the
maximum plant air demand. System controls are almost always needed to orchestrate a
reduction in the output of the individual compressor(s) during times of lower demand.
Compressed air systems are usually designed to operate within a fixed pressure range and
to deliver a volume of air, which varies with system demand. System pressure is monitored
and the control system decreases compressor output when the pressure reaches a
predetermined level. Compressor output is then increased again when the pressure drops to
a lower predetermined level.
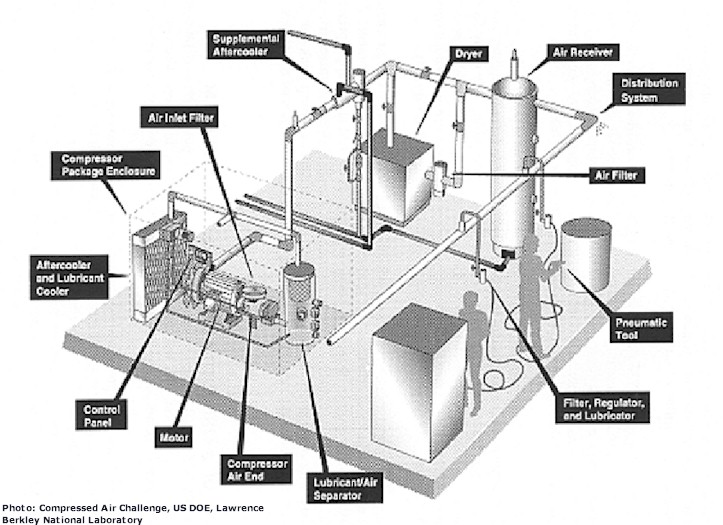
|
Compressed Air Leaks
Leaks can be a significant source of wasted energy in an industrial compressed air system,
sometimes wasting 20% or 30% of a compressor’s output. A typical plant that has not
been well maintained will likely have a leak rate equal to 20% of total compressed air
production capacity. On the other hand, proactive leak detection and repair can reduce
leaks to less than 10% of compressor output.
In addition to being a source of wasted energy, leaks can also contribute to other
operating losses. Leaks cause a drop in system pressure, which can make air tools function
less efficiently, adversely affecting production. In addition, by forcing the equipment to
cycle more frequently, leaks shorten the life of almost all system equipment (including
the compressor package itself). Increased running time can also lead to additional
maintenance requirements and increased unscheduled downtime.
Leak Detection
Since air leaks are almost impossible to see, other methods must be used to locate them.
The acoustic detector can recognize the high frequency hissing sounds associated with air
leaks. These portable units consist of directional microphones, amplifiers, and audio
filters, and usually have either visual indicators or earphones to detect leaks. A simpler
method is to apply soapy water with a paintbrush to suspect areas. Although reliable, this
method can be time consuming.
How to Fix Leaks
Leaks occur most often at joints and connections. Stopping leaks can be as simple as
tightening a connection or as complex as replacing faulty equipment such as couplings,
fittings, pipe sections, hoses, joints, drains, and traps. In many cases leaks are caused
by bad or improperly applied thread sealant. Select high quality fittings, sealed properly
with appropriate thread sealant. Non-operating equipment can be an additional source of
leaks. Another way to reduce leaks is to lower the pressure differential across an orifice
or leak; that is, lower the rate of flow, so reduced system pressure will result in
reduced leakage rates.
Stabilizing the system header pressure at its lowest practical range will minimize the
leakage rate for the system. While leakage can come from any part of the system, the most
common problem areas are: couplings, hoses, tubes, and fittings, pressure regulators, open
condensate traps and shut-off valves, and pipe joints, disconnects, and thread sealants.
Maintenance
Like all electro-mechanical equipment, industrial compressed air systems require periodic
maintenance to operate at peak efficiency and minimize unscheduled downtime. Inadequate
maintenance can have a significant impact on energy consumption via lower compression
efficiency, air leakage, or pressure variability. It can also lead to high operating
temperatures, poor moisture control, and excessive contamination. Most problems are minor
and can be corrected by simple adjustments, cleaning, part replacement, or the elimination
of adverse conditions. Compressed air system maintenance is similar to that performed on
cars; filters and fluids are replaced, cooling water is inspected, belts are adjusted, and
leaks are identified and repaired.
All equipment in the compressed air system should be maintained in accordance with
manufacturers’ specifications. Manufacturers provide inspection, maintenance, and
service schedules that should be followed strictly. In many cases, it makes sense from
efficiency and economic standpoints to maintain equipment more frequently than the
intervals recommended by manufacturers, which are primarily designed to protect equipment.
One way to tell if a system is being maintained well and is operating properly is to
periodically benchmark the system by tracking power, pressure, and flow. If power use at a
given pressure and flow rate goes up, the system’s efficiency is degrading. This
bench marking will also let you know if the compressor is operating at full capacity, and
if the capacity is decreasing over time. On new systems, specifications should be recorded
when the system is first set up and operating properly.
Source: U.S. DOE, Office of Industrial Technology Compressed Air Challenge Fact Sheets
|