Basement Walls
New Methods in Foundation Systems
Insulating Slab-On Grade Foundation
Crawl Spaces
Installation Cost and Performance
An uninsulated foundation can result in a large heat loss from an otherwise tightly
sealed, well-insulated house. It can also make below grade rooms uncomfortable. Foundation
insulation can result in lower heating requirements, and also helps in avoiding water
vapor condensation problems, which is often caused by the difference in temperature
between the basement interior and the earth around the foundation. However, a poorly
designed foundation insulation system can cause many problems such as radon infiltration,
moisture problems, and insect infestation.
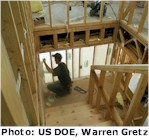 |
Basement Walls
Building scientists report that the best way to have a dry basement is to insulate the
outside of exterior walls with a rigid fiberglass type "mat." Under the mat is a
damp-proofing coating over the entire foundation, from footing to just below the finished
grade. A carefully designed perimeter drainage system consisting of washed gravel,
perforated plastic pipe, and filter fabric is also strongly recommended for locations with
poor soil drainage. A waterproof paint over the room side of the foundation wall is also
often recommended. Some foam insulations are impregnated with boric acid to discourage
termite infestation. However, the borate chemical often slowly leaches out of most
materials when exposed to ground water. Adding insulation to the interior of the
foundation is often more cost effective for an existing building. |
New Methods in Foundation Systems
Some new construction systems lend themselves to both structure and foundation insulation
at the same time. For example, an Insulating Concrete Form (ICF) system uses a rigid
foamboard applied in the middle of a cast-in-place concrete wall, or, serves as both inner
and outer concrete forms in place of steel or plywood forms. When using masonry blocks for
a foundation wall, filling the block cores with high-pressure foam works better than most
other methods of filling blocks with poured-in insulations such as polystyrene beads and
vermiculite. There are also foam inserts for the block cores. These are installed as the
blocks are mortared into place. Some concrete block manufacturers attempt to increase the
thermal resistance of their product by adding materials such as polystyrene or wood chips
to the concrete mix. Even though filling the block cavities and special block designs
improve a block wall's thermal characteristics, it doesn't reduce heat movement very much
when compared to installing insulation over the surface of the blocks either on the
exterior or interior of the foundation walls. Field studies and computer simulations have
shown that core-filling of any type offers little fuel savings since the majority of heat
is conducted through the solid parts of the walls such as block webs and mortar joints.
Insulating Slab-On-Grade Foundations
Slab-on-grade foundations are often insulated over the exterior of the footing/ slab edge,
or between the interior of the footing and slab. Often the bottom of the slab is insulated
from the earth to some extent as well. Each approach has its advantages and disadvantages.
On the exterior of the footing/slab edge, insulation reduces heat loss from both the
foundation and the slab. Sometimes a foamboard insulation is extended outward beyond the
foundation for several feet. This offers more protection to the footing from freezing. It
also allows the builder to dig a shallower footing without the risking of damage due to
frost-heaving. All exposed parts of the insulation must be covered with metal, cement, or
other type of membrane to protect it from damage. When installed on the interior of the
footing/slab, it must be vertical between the footing and slab. This protects the
insulation from insects and damage better than an exterior application while it isolates
the slab from the colder footing. Insulating under an existing slab is usually
impractical.
Crawl Spaces
How to insulate a crawl space depends on whether you vent it. Traditionally, crawl spaces
have been vented to prevent problems with moisture. However, this did not always work
well. Today, building researchers are moving toward treating the crawl space the same as
any other basement. This section will address both options. If the crawl space is to be
vented, carefully seal any and all holes in the floor above ("ceiling" of the
crawl space) to prevent air from blowing up into the house. Insulate between the floor
joists with rolled fiberglass. Install it tight against the subfloor. Cover the insulation
with a house-wrap or face the fiberglass vapor barrier down. Seal all of the seams
carefully to keep wind from blowing into the insulation. Also, adequately support the
insulation with mechanical fasteners so that it will not fall out of the joist spaces in
the years to come. DO NOT just rely on the friction between the fiberglass and wood joists
to secure it in place. Install a polyethylene vapor retarder, or equivalent material, over
the dirt floor. Tape and seal all seams carefully. You may also cover the polyethylene
with a thin layer of sand or a thin slab of concrete to protect it from damage. Do not
cover the plastic with anything that could make holes in it, such as crushed gravel. Be
sure the head-room of the crawl space meets local code regulations if you are considering
pouring a concrete slab. If the crawl space is to be unvented, seal all holes in the
foundation where outside air can enter. Install the plastic ground cover as described
above for an unvented crawl space. Run the plastic up the walls and attach it to the first
piece of wood (the mudsill). Install rigid insulation foamboard against the foundation
from the subfloor to the plastic (or concrete slab) on the floor of the crawl space. Do
this all the way around the perimeter of the foundation. An alternative to foamboard is to
drape fiberglass roll insulation down the foundation walls with the edges butted tightly
together. This is an acceptable alternative to foamboard insulation as long as the crawl
space stays dry.
Installation Cost and Performance
Although you can achieve considerable savings in space conditioning costs by insulating
the foundation, the installation costs can become relatively high, especially for retrofit
projects. The type of materials used, the application method, and the extent of work all
affect the overall cost. Simple payback is typically in the range of 6 months for a simple
do-it-yourself installation to 20 years for "professionally" installed and more
involved work. Adding foundation insulation during new construction is usually less
expensive.
Source: U.S. DOE, Energy Efficiency and Renewable Energy Network, Consumer Energy
Information: EREC Reference Brief. EREC is operated by NCI Information Systems, Inc. for
the National Renewable Energy Laboratory/U.S. Department of Energy. The content of this
brief is based on information known to EREC at the time of preparation. No recommendation
or endorsement of any non-U.S. Government product or service is implied if mentioned by
EREC.
|